JGB Extruded-Through-the-Weave Hose Technology
At JGB Enterprises we pride ourselves on supplying the highest quality, and most technologically advanced hose and assemblies the market has to offer, and our lay flat hose program is no exception. Our EAGLE "TPU" Thermoplastic polyurethane and EAGLE "NBR" Nitrile rubber hoses are produced using a state of the art manufacturing technique referred to as, "extruded-through-the-weave" or single extrusion.
The unique "extrusion through the weave" process eliminates the use of tubes and adhesives. The compound is fed into a heated extrusion barrel it’s extruded through the woven reinforcement jacket as it’s drawn through the channel. This one step extrusion process results in an extremely strong homogenous bond between cover and woven reinforcement jacket.
EAGLE TPU hose is produced with Huntsman polyurethane U.S.A: Specification IROGRAN® A 85 P 4394
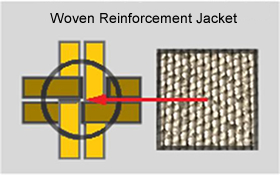
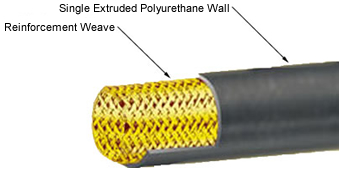
Advantages of through-the-weave construction:
- No adhesive is used; hence, there is no potential for the hose to delaminate.
- At working pressure, through-the-weave hose has an elongation rate of less than 1%.
- Adhesion peel tests have shown that adherence of a through the weave hose is twice as strong as that of 3-Ply.
- The interior of through-the-weave hose is much smoother than 3-Ply hose, thus affording a higher flow rate.
Disadvantages of the 3-Ply layered construction:
- 3-Ply manufactures must apply pin holes to the outer cover to allow steam used in the gluing process to escape, those same pin holes could allow moisture to reach the adhesive that binds the outer layer to the reinforcement jacket. While this should not cause the inner tube to leak per se, moisture would reduce the adhesive bond between both the outer and the inner tubes and the reinforcement jacket. Separation from the reinforcement jacket would mean a loss of integrity in the strength of the hose and in the worst case a rupture, the location and extent of which cannot be predicted.
- At working pressure, 3-Ply hose can reach an elongation rate as high as 10%. Such elongation results in "snaking" which causes the hose to move in an unpredictable manner and may lead to damage to the hose and the environment, as well as a reduced flow rate. Not to mention the time lost shutting down to relay.
- Also less Poly/rubber may be used in the manufacture of 3-Ply hose because of an incentive inherent in the manufacturing process to keep the hose tubes as thin as possible. This results from the necessary procedure of turning the inside tube out, which becomes very difficult if the tubes are too thick. While suppliers of 3-Ply hose will no doubt at tribute a thinner wall to a manufacturing process finely tuned to using only the amount of material necessary to provide the desired outcome, the truth is that a thinner tube has been used to accommodate the manufacturing process. Thinner wall will puncture easier and wear faster.